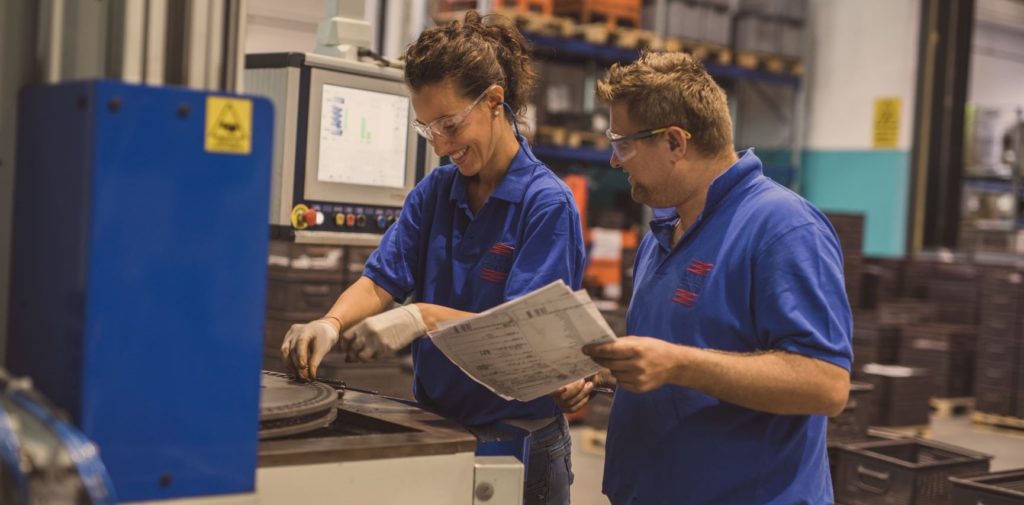
Molle Industriali Conte was founded in 1953 and produces high precision springs for technologically advanced industry sectors such as automotive, computers, and aerospace. Molle employs around 70 workers and has been SA8000-certified for over 15 years, since 2003.
Seeing the Internal Value
Molle initially sought SA8000 certification not because of outside demand or pressure, but because management saw the potential internal value of certification. Management saw improving their social performance as a “cost and consequence of respect of rules.” They believed that SA8000 could bring substantial internal value through a healthy working environment, increased salary, and worker commitment.
Business As Usual
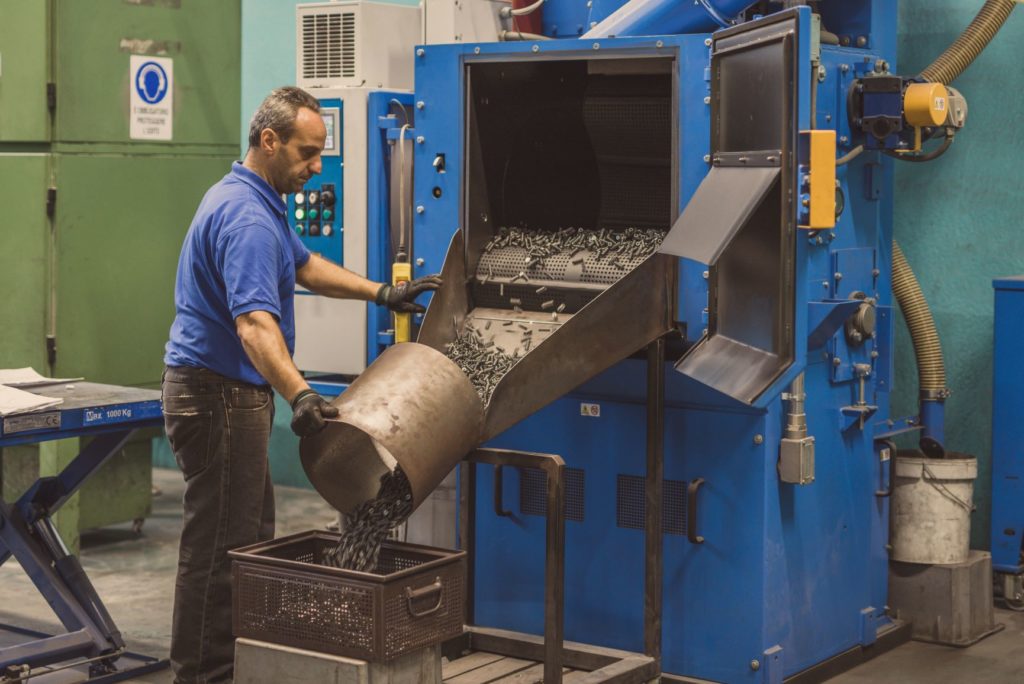
In the years since certification, their assumptions have been validated. As their systems matured, SA8000 became a vital part of the way Molle does business. Social performance is part of their business structure, with SA8000 goals and evaluation requirements integrated into business planning at the highest level. Workers are kept informed on performance, constantly involved in business management, and receive ongoing updates on trends and new directions for the company. Molle has seen increased productivity and extremely low absenteeism and employee turnover rates. Molle has also found SA8000 valuable for communicating with external stakeholders, especially with buyers interested in the certificate. SA8000’s reputation and it’s robust oversight program, allows Molle to quickly communicate the company’s values and commitment to good labor practices.
Good Practice: Systematic Approach to Continual Improvement
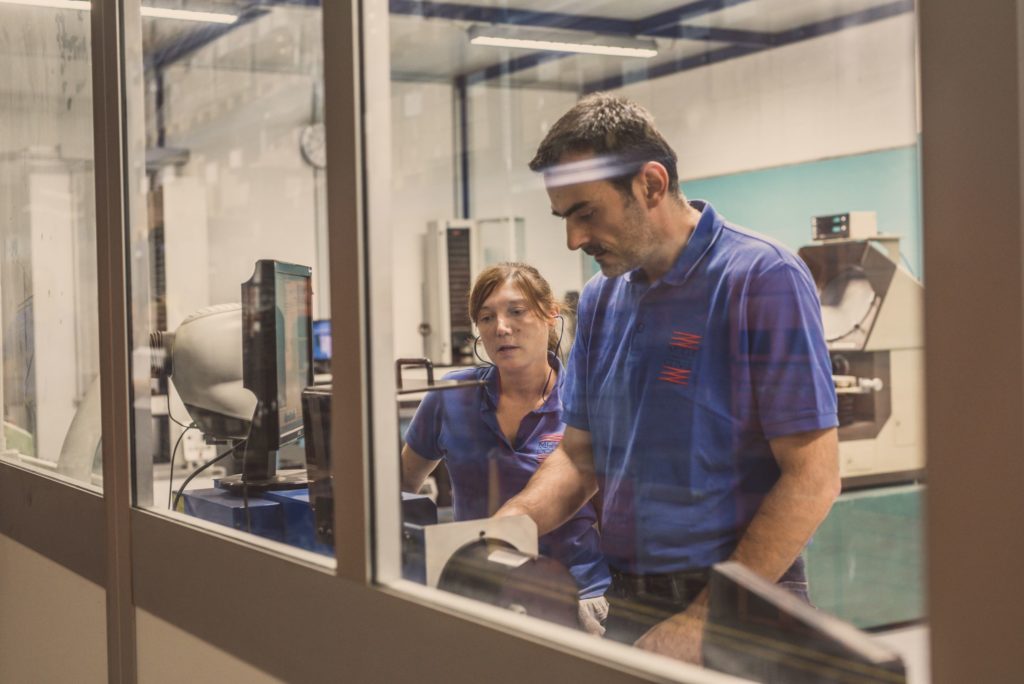
One way Molle has leveraged SA8000 to benefit their business is by using a centralized system to more accurately measure performance and encourage data-driven improvements. Using a popular project management software, Molle translated the SA8000 Standard into Key Performance Indicators (KPIs)–data points that express progress on performance. For example, to track remediation efficacy, one KPI may be the number of complaints closed with a satisfactory result for all actors.
Molle’s KPI tracking system has facilitated a systemized approach to improvement. Because they measure and track important indicators in a centralized location, Molle can see where their performance is lacking, where processes are failing, and where their efforts are succeeding. It allows reporting against performance within the management team, with stakeholders, and with workers.