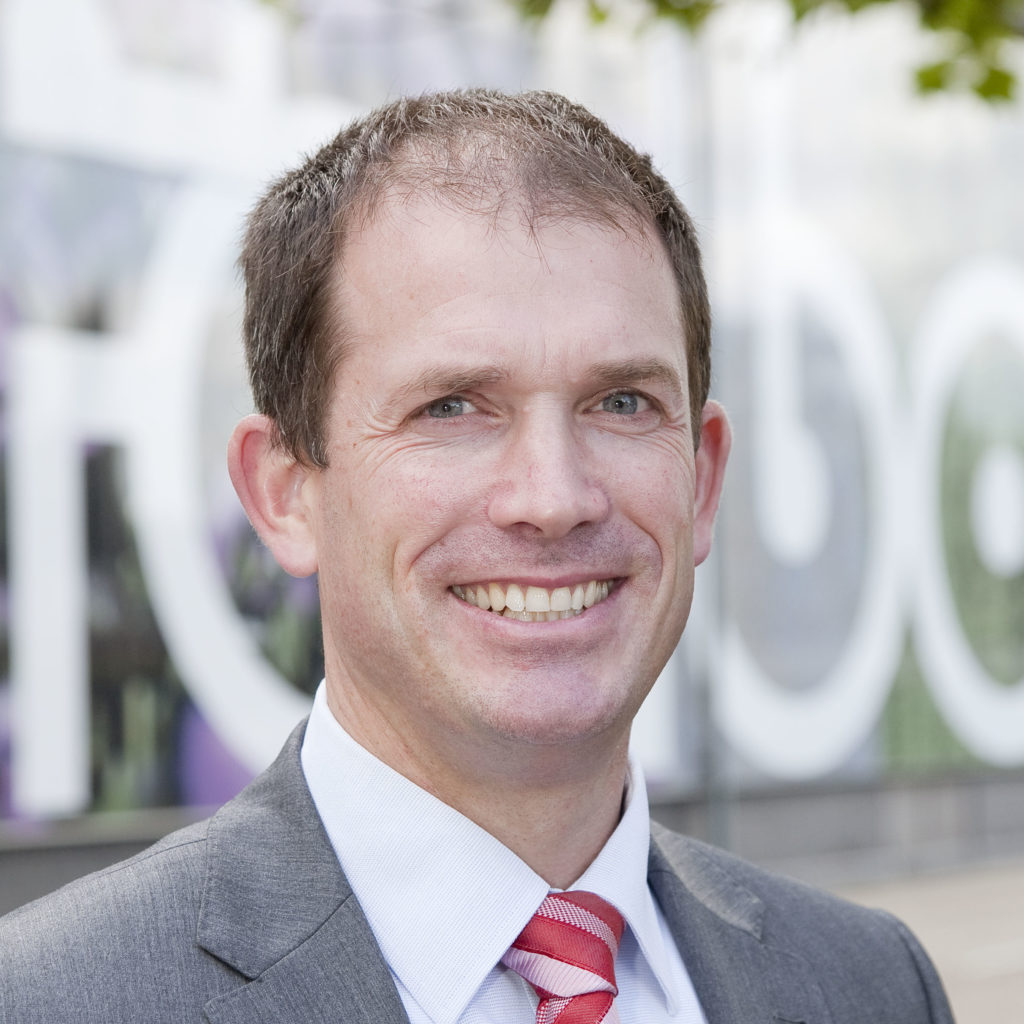
Forbo Flooring first achieved SA8000 certification in 2012. This is an interview with Forbo Flooring HR Director, Joost Dirkx.
This interview was conducted in 2015. We are pleased to say Forbo Flooring is still reaping the benefits of certification when this interview was re-posted in 2020.
SAI: Can you tell us about Forbo Flooring Systems, and how you first came to think about responsibility in your sourcing?
Joost Dirkx (JD): Forbo Flooring Systems originates from 1928 and today is a world leader in high quality, commercial floor coverings. We provide our customers with sustainable flooring solutions with our main products such as linoleum, which is the most sustainable flooring covering in the world. Flooring Systems is committed to sustainability and “creating better environments” for not only the environment, but to shareholders, customers, and other stakeholders like workers in their supply chain. We have implemented SA8000 Standard for our social dimensional sustainability and integrated it as part of our management system.
We have always been committed to sustainability and focus not only on the environment, but we have also extended this to the human aspect of sustainability. Many of Forbo’s production workers were a bit surprised when they found out that SA8000 was being implemented and were not sure why this was being done initially because there are already compliance laws. However, SA8000 moved this idea towards suppliers. When this news was spread, people understood and agreed this was the right thing to do. Forbo Flooring Systems has always been committed to sustainability and everyone expects us to do the right thing.
SAI: Your website states that all Forbo Flooring Systems’ products sold in the UK, with the exception of Colorex, are manufactured in an SA8000-certified facility. Can you speak more to this?
JD: Yes, and actually not only is this the case in the UK, but also for Netherlands and France. Our factories became SA8000 certified in France in 2012, and gradually expanded to the Netherlands earlier this year.
SAI: What are some of the positive changes you have seen since in facilities since becoming SA8000 certified? What are some of the biggest challenges of social compliance in this industry? Are there any specific difficulties you faced when trying to achieve compliance?
JD: We tried to leverage what we learned in France to achieve certification and extend it to other places. Most of our changes were primarily concentrated on our purchasing policy, as it was done on a global level. When we pursued certification for France, we changed our purchasing policy to include SA8000 criteria and required the supplier side to commit as well. There were no significant changes on our production process in the UK and Netherlands but overall, communication of the Standard to our suppliers was the hardest and most critical part we had to focus on and to convincing them. We continue to make continuous improvements.
SA8000 accreditation can help spread the word on sustainability and help tell the world how committed we are.
SAI: Were there any specific methods of communication regarding SA8000 that you found to work or not work?
JD: We had different methods of communication: specifically towards our employees and then specifically to suppliers. For example, we developed an e-learning course that was translated into local language for all of our employees. In terms of our external communications, we used the abridged guidance document of SA8000 and gave it directly to them during conversation. We also gave a short PowerPoint presentation on SA8000 and our purchasing documentation.
We were a bit surprised that there are not many standard eLearning trainings available on the market. We developed an employee e-learning course to teach our employees about the Standard, which 80% of all relevant employees have completed. We have received many positive comments and found this to be a very effective way of communication. Of course, this is only one way. We also used flyers, brochures, posters, etc.
SAI: Would you recommend implementing SA8000 to other businesses? Why?
JD: Absolutely. SA8000 is an accredited standard and it is well known within certain types of industry and with newer types of industry such as building and construction—it fits our needs extremely well. The SA8000 Standard certification is a nice addition to the rest of the management systems we have related to the environment such ISO 14001 and Health and Safety through OHSAS 18001 and other standards. We understand that the auditing process takes quite some resources. For the future, we would expect a combined standard for more efficiency.
We also believe that SA8000 gives us a competitive advantage for customers. We do have some customers that really appreciate our work towards sustainability and that range of customers is expanding. We also assume we get more business because of the Standard. More and more customers are looking for sustainable options and respectable suppliers. It’s not only the right thing to do, but it helps our business.
SAI: How did you hear about SA8000?
JD: I think it goes back more than 5 years ago. At that time, we were looking at different standards and came across SA8000. We started using SA8000 as early as 2010.
SAI: Is there anything else you want people to know about Forbo Flooring Systems?
JD: Forbo Flooring Systems has always been committed to creating better environments, committed to the health of their own employees, the health of workers in the supply chain, and toward customers. It’s just something we value highly but sometimes are too modest to tell everyone. SA8000 accreditation can help spread the word on sustainability and help tell the world how committed we are.