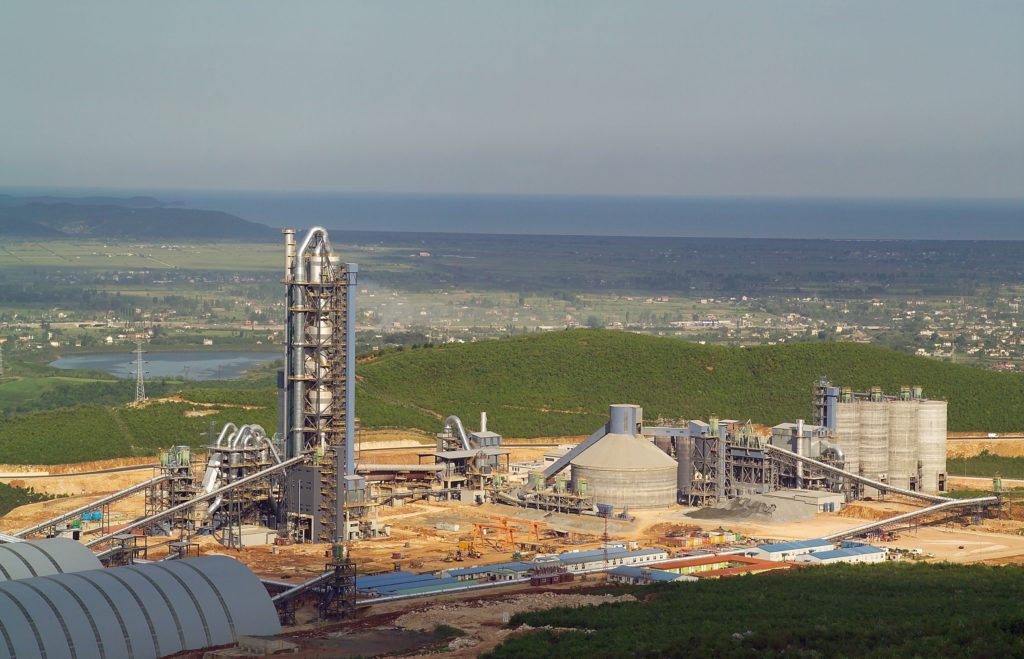
Interview with Saka Teuta, CSR Administration Officer, at Antea Cement
In 2012, ANTEA Cement, a subsidiary of TITAN Cement of Greece, became the first SA8000-certified company in Albania. This interview was conducted in 2013, but we are proud that Antea is still SA8000-certified when this interview was re-posted in 2019.
SAI: Tell us a little about the background of Antea Cement.
Saka Teuta (ST): In 2010, TITAN Group (a cement manufacturer headquartered in Greece), along with the International Finance Corporation (IFC) and the European Bank for Reconstruction and Development (EBRD) collaborated in the biggest Greenfield investment in Albania to create Antea Cement SH.A.
The company is recognized for its performance and genuine commitment to Corporate Social Responsibility. It has adopted the principles of sustainability in its daily operations: through Integrated Management Systems (BS OHSAS 18001, ISO 9000 & ISO 14001); by joining as a founding member of the national CSR Network; and through being the first and only business in Albania certified for its work standards by SA8000.
SAI: What were your motivations in deciding to pursue SA8000 certification?
ST: ANTEA Cement, as part of TITAN Group, has the same principles and guiding values with its mother company. The Group is voluntarily committed to Corporate Social Responsibility and Sustainability principles and has embedded them into its operations. We firmly believe as a company that this kind of operations is not only an ethical issue but also a good way for doing business.
Compared with other companies in Albania, ANTEA Cement is among the few which has had in place an Integrated Management System comprising Health & Safety Management System (OHSAS 18001), Environment Management System (ISO 14001) and Quality Management System (ISO 9001). The inclusion of SA8000 in the Integrated Management System of ANTEA Cement was seen as a prerequisite by our shareholders for a multinational company respecting in practice its employees’ human and working rights in a country where many companies have issues in complying to internationally set human rights regulations and standards. Therefore, ANTEA Cement accepted willingly the responsibility of raising the standards in the area of human rights in Albania by means of the certification.
SAI: What are some positive changes you have seen in the facility since becoming SA8000 certified?
ST: ANTEA has tried to make the right steps in every field from the beginning, but of course improvement is a continuous effort of all in the company. So, by achieving the SA8000 certification, we saw positive changes in the perception of employees towards topics related to Health & Safety and Environment, as well as increased awareness of our employees, contractors, and also local communities accomplished through continuous training.
Our absenteeism rate is low only due to the fact that Antea offers to people the safe, healthy, and stable working environment they are looking for.
Another positive change we have noticed is the involvement of our employees in suggesting ideas and making their comments for any issue, and this because they have their own representative who is present in every management meeting of the system and member of the Social Accountability Board that is conducted by the company’s managers.
SAI: What were the difficulties your company faced when pursuing SA8000 certification and how did you resolve them?
ST: Our biggest difficulty was to achieve compliance with SA8000 by our contractors. In some of the cases, new requirements are translated to additional cost [for them]. So we are in continuous and close cooperation with our contractors by consulting, training, and monitoring to ensure their compliance with the standard, because ANTEA Cement cares not only for providing a good working environment for its own employees, but for anyone that works with us.
SAI: What are the biggest challenges of social compliance in the cement manufacturing industry?
ST: The challenges that a cement plant faces are both social and environmental. In general, the biggest challenges of social compliance in [heavy] industries include failure of declaration of employees for the social and health contributions, excessive overtime, payment of overtime not at a premium rate, low standard of local suppliers and contractors, and no clear procedures during termination of employment.
Also, ANTEA Cement has put an effort in order to change the most common perception in Albania that only men can be employed in a cement industry, by giving equal opportunities to female engineers to become a part of our team.
SAI: Where does your workforce come from?
ST: At this moment, ANTEA Cement has 200 direct employees. 43% of them come from the communities around our plant and the rest from other areas of the country. A very small percentage of our employees are expatriates, which are highly specialized professionals in positions our local personnel were not ready to fill at the time we constructed the plant.
ANTEA Cement has opened a Technical School where youngsters from the local community can be trained for technical skills in order for them to allow more potential for employment. Regarding direct employees, a training procedure is in place which gives our employees opportunities for professional development on respective areas of expertise.
SAI: What was the feedback from workers after the facility was SA8000 certified? Did you see an improvement in worker satisfaction?
ST: Our main employees’ feedback was that they feel very proud working for a company which sets as one of its main priorities the advancement of the human rights at work, and the protection of the basic human rights of workers through following the highest international standards.
Their enthusiasm was also evident through the increase of their active participation to many voluntary company’s social responsibility initiatives and activities, like for example those addressed to the local community (e.g. cleaning of some areas, blood donation, etc.).