SAI’s FairCapacity Program seeks to reduce labor risks in the apparel industry through responsible subcontracting, better production planning and transparency. As the European Union-funded program wraps up in Bangladesh, we explore the relationship between production capacity planning and forced labor in apparel supply chains and how FairCapacity has worked to address it. This is the first of a two-part series reflecting on outcomes and takeaways from the FairCapacity project.
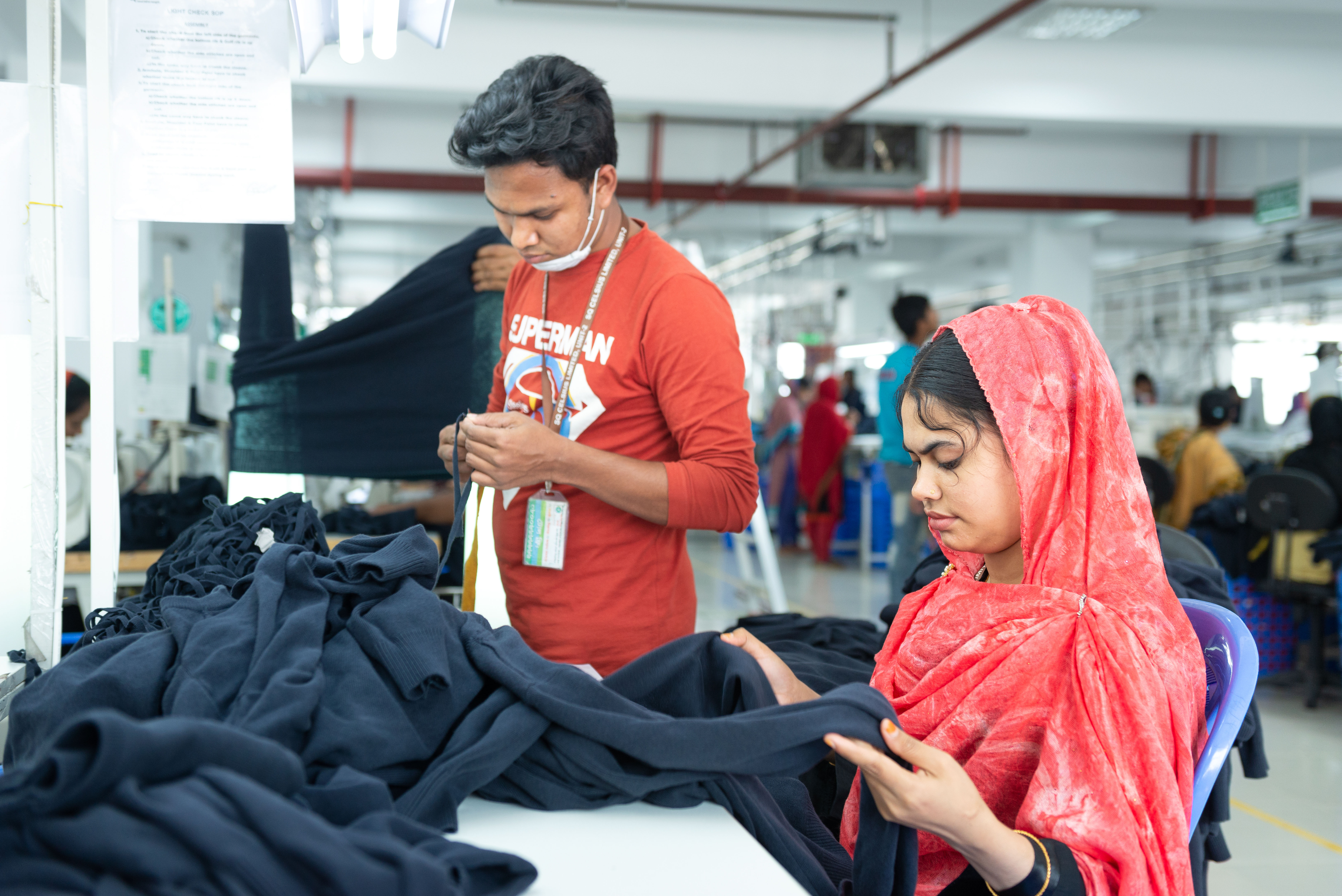
Forced labor in the global garment industry is a byproduct of its competitive and fast-paced nature. Factories must operate at close to full capacity at all times and make themselves available for multiple buyers to be competitive. Under these conditions, they easily become overextended; poor production capacity calculations are a contributing factor. Currently, most suppliers use “back of the envelope”, essentially informal, estimations to calculate their production capacity. Among Bangladesh garment suppliers we interviewed for the FairCapacity project, SAI found that 100% knew they were not measuring their capacity accurately.
These inaccurate calculations result in suppliers setting unrealistic production targets, to which brands and retailers add price, time, and volume pressures without realizing that factories are already overstretched. Factory managers often have to sacrifice other important considerations—including labor compliance, quality, and investment in future improvements—to make ends meet. This means that the costs of doing business are ultimately borne by workers.
Factory managers often have to sacrifice other important considerations to make ends meet. This means that the costs of doing business are ultimately borne by workers.
Industry pressures create risks for workers
An extremely common tactic is excessive overtime—both one of the most prevalent and most overlooked ILO indicators of forced labor. It is so normalized that people working excessive hours typically do not identify as being victims of forced labor, even though it has a negative impact on workers’ health, safety, and well-being, leading to cycles of long hours, lower productivity, and lower hourly wages.
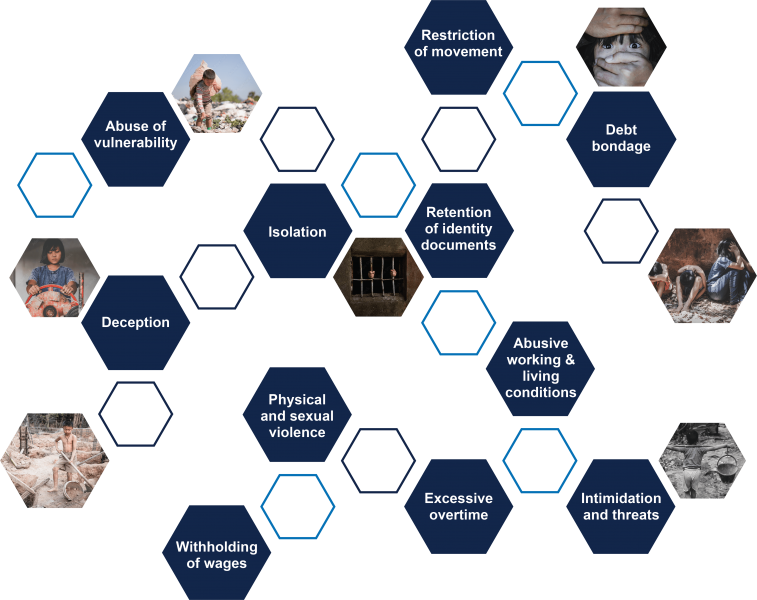
Another common tactic is using unauthorized subcontractors, often informal factories. Because they are much less likely to participate in labor audits and because their workers are not eligible for social protections tied to employment, risks of forced labor increase exponentially in these and other facilities upstream in the supply chain. One study of informal factories in Bangladesh’s garment manufacturing hubs found that over 86% of workers met the ILO criteria for forced labor. The impacts of Covid-19 have also disproportionately impacted informal workers, exacerbating many of these risks.
Unauthorized subcontracting represents an inherent risk to buyers, circumventing their usual quality control, social compliance, environmental, and other oversight systems. Many buyers, therefore, have strict policies against subcontracting or require extensive and time-consuming review processes to approve a subcontractor. This strategy does little to prevent subcontracting in light of the industry’s unpredictable and demanding nature. Instead, many suppliers bypass buyer approval systems and use unauthorized subcontractors to complete orders on time, further obscuring these operations from potential oversight.
Better Production Calculation and Planning Address Common Risk Factors
Better production capacity calculation and planning can help disrupt the vicious cycle of overbooking, overtime, and subcontracting that puts millions of workers at risk of forced labor each year. In our FairCapacity Program, SAI conducted detailed studies of garment factory operations in Bangladesh and identified over 20 variables that affect production capacity. Working closely with suppliers, we determined that 15 of those are crucial variables that must be included for accurate capacity calculation, including accounting for average disruptions due to strike and unrest, machine breakdown, worker turnover, number of workers at various skill levels and more. Based on these findings, SAI developed an algorithm and simple calculator tool, making it easy for managers to apply the calculation in their factory.
When suppliers have better information about their true capacity and when they have tools and training to make better business decisions based on that knowledge, they can reduce their reliance on excessive overtime and unauthorized subcontracting to complete orders on time. FairCapacity tools for workflow mapping and management allow managers to see more clearly whether they will be able to cover potential orders in a given timeframe and cost-benefit analysis tools can help them decide whether orders that will require overtime or subcontracting are worth the additional cost.
Especially as buyers become more aware of the effect their purchasing practices have on workers and are being held more accountable for those impacts, this information may also improve suppliers’ ability to negotiate price points and lead times, giving them greater leeway to invest in health and safety and other workplace improvements.
Ultimately, it will take better coordination and communication from both sides of the supply chain to eliminate forced labor in the garment industry. More accurate and reliable production capacity calculations and planning are one piece of a larger effort that is needed to build greater trust and transparency in supply chains. We look forward to sharing more about how the FairCapacity Program has contributed to this larger effort in the next article in this series.