A TenSquared Case Study
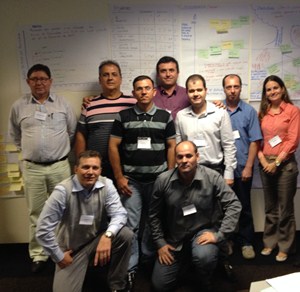
Company Profile
Company: Ajinomoto
Country: Brazil
Industry: Chemicals and Food & Beverage
Highlights
Goal: Reduce the exposure points and risk of burn situations by 70% in all sites.
Methods:
- Identifying low-cost solutions that allowed them to address more risks with less money
- Communicating all changes to workers to ensure full understanding
- Empowering workers to make their own suggestions
Results: Surpassed goal, eliminating 90% of 207 total identified exposure points
Case Study
«We have had a lot of projects at our company, but this project went deeper—it produced a lot more results and brought a lot more creativity to the area of Health and Safety.»
TenSquared Worker Participant, Ajinomoto Brazil
At the beginning of their TenSquared journey, Ajinomoto identified accident prevention as their challenge area and then conducted a risk assessment of the workspace to identify specific hazardous areas and burn exposure points. Through this exercise, the Ajinomoto TenSquared team identified 207 potential burn-exposure risk points in the company’s plant. Their ambitious goal was to eliminate 70% of those risks within 100 days.
The team worked together to implement a work plan, which would ultimately eliminated 90%, or 186, of the exposure points, surpassing the original goal by 20%. Some of the measures the team took to generate these impressive results included:
- Introducing new signage
- Modifying transport paths and operations
- Restricting certain areas
- Using fiberglass isolation tape to cover exposed pipes
One low-cost solution to reducing exposure was to wrap fiberglass isolation tape (which costs 72% less than traditional heat isolation techniques) around exposed pipes. Not only did this solution save money, it drastically reduced workers’ exposure to burn risks in the plant.
The team also communicated with workers about these changes to ensure that all workers were aware of the changes, understood the new safety procedures, and felt empowered to offer up additional ideas.
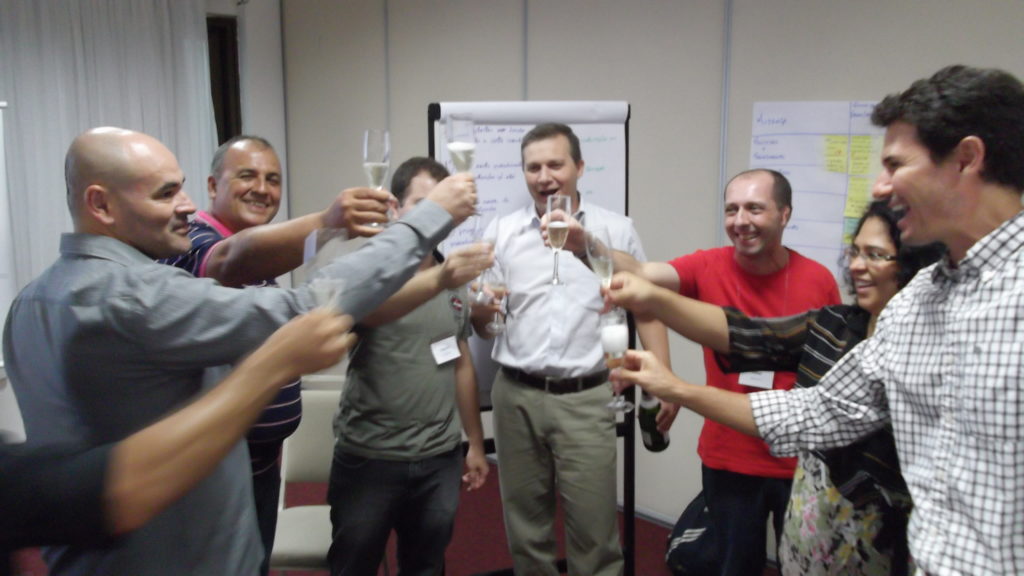
What is TenSquared?
Find out how SAI’s innovative 100-day worker engagement and capacity-building program can help your company address root causes of workplace issues, overcome institutional hurdles to change, and foster a culture of continual, sustainable improvement.