A TenSquared Case Study
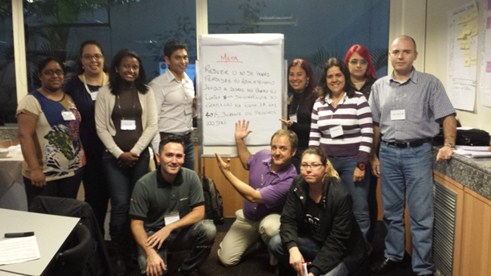
Company Profile
Company: Flextronics
Country: Brazil
Industry: Electronics
Highlights
Goal: Reduce absenteeism due to body pain/ache or injuries by 40%
Methods:
- Identified “problem areas” with high levels of risk and targeted those areas for improvement
- Made multiple small, low-cost changes to tackle the problem
Results:
- Goal Achieved, decreased risk of injury pain from repetitive motions, leading to a 40% decrease in absenteeism
- Saved company $120,000 annually
Case Study
Ergonomic risk is not always taken seriously—considered in some cases to be about comfort rather than health—but poorly designed work processes (e.g. repetitive motions or misaligned work stations) are a common cause of workplace injury.
Flextronics decided to target ergonomic risk as their TenSquared challenge area. They began by creating an ergonomics committee, which surveyed workers to assess ergonomic risks in the company. They were able to identify a key area of risk on one assembly line in particular.
Based on that information, the committee set about making minor physical changes to the workspaces to enable workers to perform their tasks with less risk of injury. Some of the changes they made include:
- Changing the set‐up of the line
- Adding a platform that allowed workers of different heights to adjust their desk to the correct height to prevent muscle strain or improper alignment
- Changing tray sizes and the positioning of handles to create a more ergonomically sound arrangement
These changes resulted in the team achieving their TenSquared goal: reducing absenteeism due to workplace injury by 40%. The reduced absenteeism was also a boon for business, saving the company $10,000 per month, or $120,000 over the course of one year!
What is TenSquared?
Find out how SAI’s innovative 100-day worker engagement and capacity-building program can help your company address root causes of workplace issues, overcome institutional hurdles to change, and foster a culture of continual, sustainable improvement.