A TenSquared Case Study
Company Profile
Company: Chicony
Country: China
Industry: Electronics Manufacturing
Highlights
Goal: Identify and resolve seven risks related to chemicals in 100 days:
Methods:
- Conducting root cause analysis
- Designing their own tools and materials to create tailored, inexpensive solutions
Results:
- Identified and resolved seven chemical risk areas, achieved or surpassed all sub-goals
- Sub-goal 1 surpassed: Reduced the chemical consumption for cleaning by 62.88%
- Sub-goal 2 achieved: 100% of chemicals used by employees have SDS available
- Sub-goal 3 achieved: 100% of employees have access to and wear PPE
- Sub-goal 4 achieved: 100% of employees using chemicals were trained
- Sub-goal 5 achieved: Employee’s direct skin contact with chemicals eliminated
- Sub-goal 6 surpassed: Achieved 96.4% employee satisfaction on ventilation, an improvement of 220%
- Sub-goal 7 achieved: Reduced worker exposure to chemicals by 90%
- 71% of workers said management was more open to worker suggestions
Case Study
Workers in electronics production facilities around the world are frequently exposed to chemicals, including highly toxic ones. Chemicals can be used in the manufacturing process and/or they can be contained within the several hundreds of components that make up an electronics product.
As a manufacturer of keyboards, Chicony workers frequently use chemicals—especially for cleaning keyboards—and management identified chemical safety as their top occupational health and safety priority. Said one Chicony worker, “It is very common for electronics factories to have a smell of chemicals and the smell has traditionally been the first thing you notice when you step into our factory. The smell has been very strong and ventilation has been a big problem for us.”
A manager described another concern related to chemicals in the factory: ”workers always used a cloth to clean the keyboards, and this meant that they had direct skin contact with the cleaning chemicals.”
During the TenSquared launch workshop, Chicony’s TenSquared team identified seven total risks associated with chemical safety that they wanted to address. Typically, TenSquared teams select one very specific risk and create a goal to solve that risk. However, Chicony wanted to challenge themselves to resolve all seven risks.
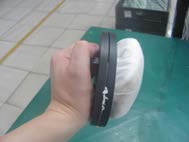
A Chicony manager described the process taken to address one of the team’s goals and the business benefit that solution brought: “We wanted to eliminate direct skin contact with chemicals, so we came up with our own tool. The first prototype of the tool was too big and too heavy, so we made a second prototype that was smaller and lighter. Now everyone uses our tool and it cleans the keyboards faster and uses less chemicals. Making our own tool is also cheaper than the clothes we used to use – this alone will save us RMB 1,920 (USD 291) per year.”
In the end, Chicony achieved or surpassed all seven of their goals. The methods they used included:
- Collecting and analyzing data on production capacity and chemical consumption in cleaning areas to conduct root-cause analysis of chemical consumption
- Designing new handheld cleaning tools to prevent skin contact with chemicals
- Making physical improvements to the workspace:
- Adjusting the oil output and air pressure of the balance bar machine, thereby reducing chemical consumption
- Designing a new circular-shaped ventilation device
- Improving ventilation ducts
- Improving airflow rate
- Implementing a system for covering screen-printing machines when not in use
- Began storing chemicals in anti-explosive cabinets and self-priming containers
- Creating a new, more easily accessible PPE station for workers
- Reviewing and updating SDS database for all chemicals
- Conducting staff training, including:
- Training on chemical management
- Training on the importance of personal protective equipment (PPE) and how to use it
- Designing, developing, and delivering custom training for chemical operators
- Conducting daily checks of PPE accessibility and use
- Conducting worker surveys
Following the project, 91% of workers agreed that TenSquared benefited everyone in the factory and 71% agreed that managers became more open to worker suggestions following the program.
What is TenSquared?
Find out how SAI’s innovative 100-day worker engagement and capacity-building program can help your company address root causes of workplace issues, overcome institutional hurdles to change, and foster a culture of continual, sustainable improvement.