A TenSquared Case Study
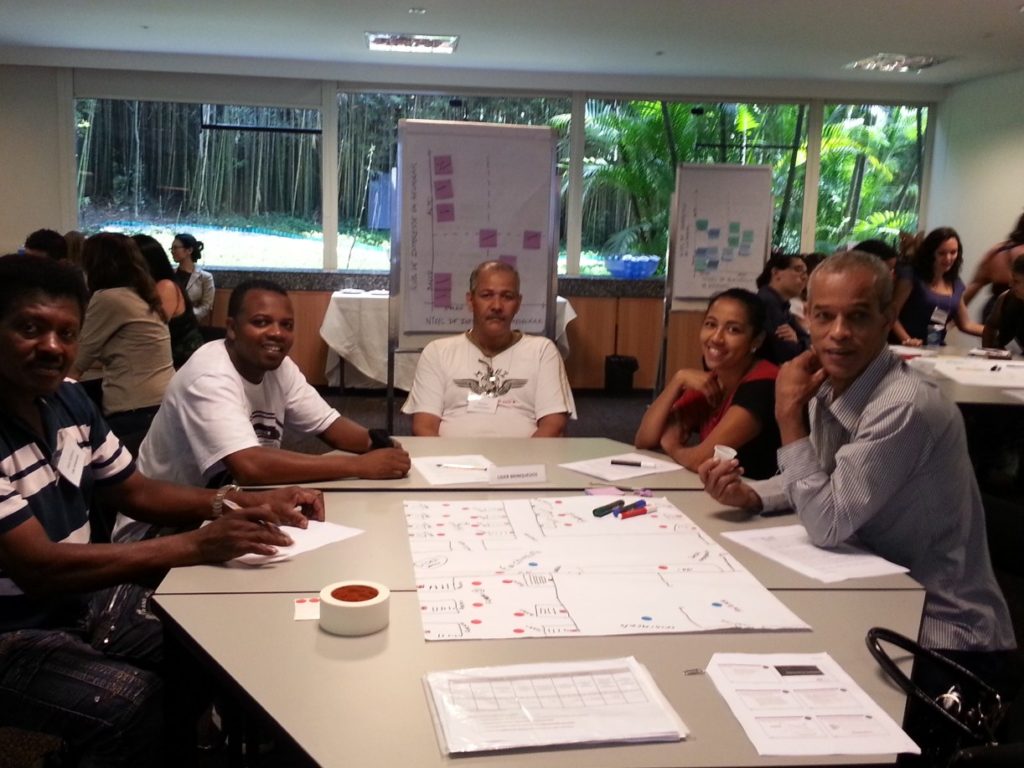
Company Profile
Company: Líder Brinquedos
Country: Brazil
Industry: Toys
Highlights
Goal: Reduce the average temperature in the areas of molding and filling to 25º
Methods:
- Tackled an old problem with a fresh approach to problem solving
- Improvised using available materials to avoid high-cost solutions
Results:
- Achieved goal of reducing facility temperature to 25°C
- Overcame institutional hurdles to change
- Saved company approximately $12,000 in facility upgrades
Case Study
The Brazilian company Líder Brinquedos had been trying to lower their ambient workplace temperature for over 10 years with no success. In midday, the temperature near the ovens in the facility would often reach 102°F, creating an uncomfortable work environment and causing risk to workers in the area.
TenSquared helped Líder Brinquedos break down their preconceived notions about problem solving within their organization. Over the course of their 100-day project, TenSquared coaching empowered workers and managers to work as a team to develop new solutions to an old problem.
Their biggest breakthrough was an act of improvisation. The team used recycled materials from the facility to create a ventilation system, which successfully decreased the workplace temperature by 25°F for a quarter of the cost of a new system.
In addition to the recycled ventilation system, the team created and implemented a worker comfort and safety checklist (including daily temperature measurements) for staff working in high‐temperature environments and installed drinking fountains with cold water to help prevent employee dehydration.
These changes not only created a significantly more comfortable work environment—which is shown to reduce absenteeism and increase productivity—they also saved the company from having to buy new ventilators—a cost-saving of about $12,000.
What is TenSquared?
Find out how SAI’s innovative 100-day worker engagement and capacity-building program can help your company address root causes of workplace issues, overcome institutional hurdles to change, and foster a culture of continual, sustainable improvement.